A version of this story appeared in the fall 2019 issue of Uncommon Path.
The Flexlite Air story begins with a problem: how to create a camp chair that weighs just 1 pound. Why a pound? For the luxury of a real camp chair, backpackers told REI they’d be willing to carry an extra pound, but no more. “But less is more difficult,” says Jon Arruda, REI senior product designer. “To execute that simplicity is hard work.”
Arruda and Steve Moenaert, REI product development engineering manager, hit multiple dead ends until they realized they might already have the solution: the existing REI Flexlite chair. The older model was 12 ounces over the target weight, so Arruda and Moenaert disassembled it, weighed every part and set the goal of slashing each component’s weight in half.
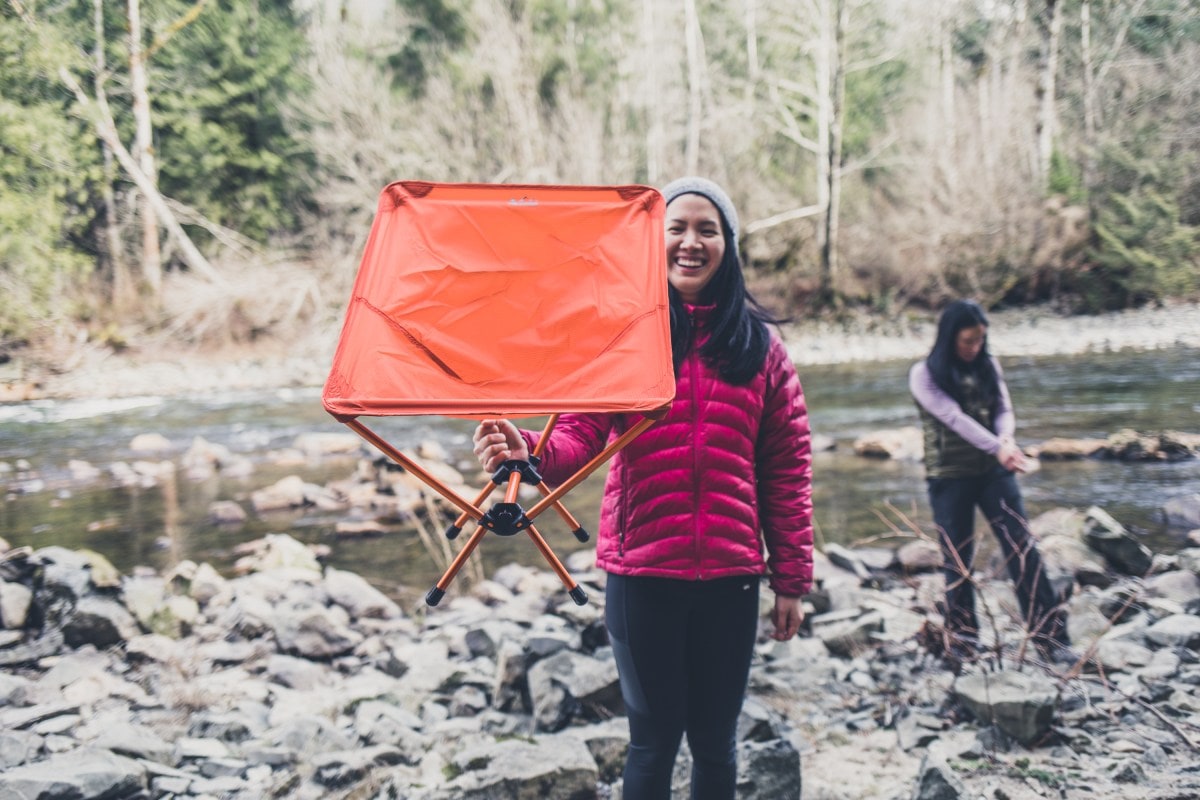
The seat of the Flexlite Air is crafted out of one piece of fabric, a concept borrowed from ship sails and parachutes.
They deployed computer-aided design to turn 2D drawings into 3D computer renderings and built prototypes, which were sent to the Magnusson Lab, REI’s custom testing facility. There, engineers scrutinized every element—seams, legs, weight capacity, the works. When a test revealed a failure, the sample was tweaked and sent back for evaluation. Wash, rinse, repeat. “We found every problem we could think of, and we tested every point,” Arruda says. “It’s more than just a chair; it’s what it represents.”
The storybook ending? The comfortable, durable, single-pound Flexlite Air. It’s a ripstop-nylon-and-aluminum piece of furniture with a 250-pound capacity whose simplicity belies the precision of its design. It’s good for the backyard as well as the backcountry. It might be just a chair, but in a certain ineffable way, it’s also a small victory for problem solvers everywhere.